D3O Insights
D3O technology is used worldwide by soldiers, professional athletes, industrial workers and people like us. Take a look at the latest features and interviews about D3O below.
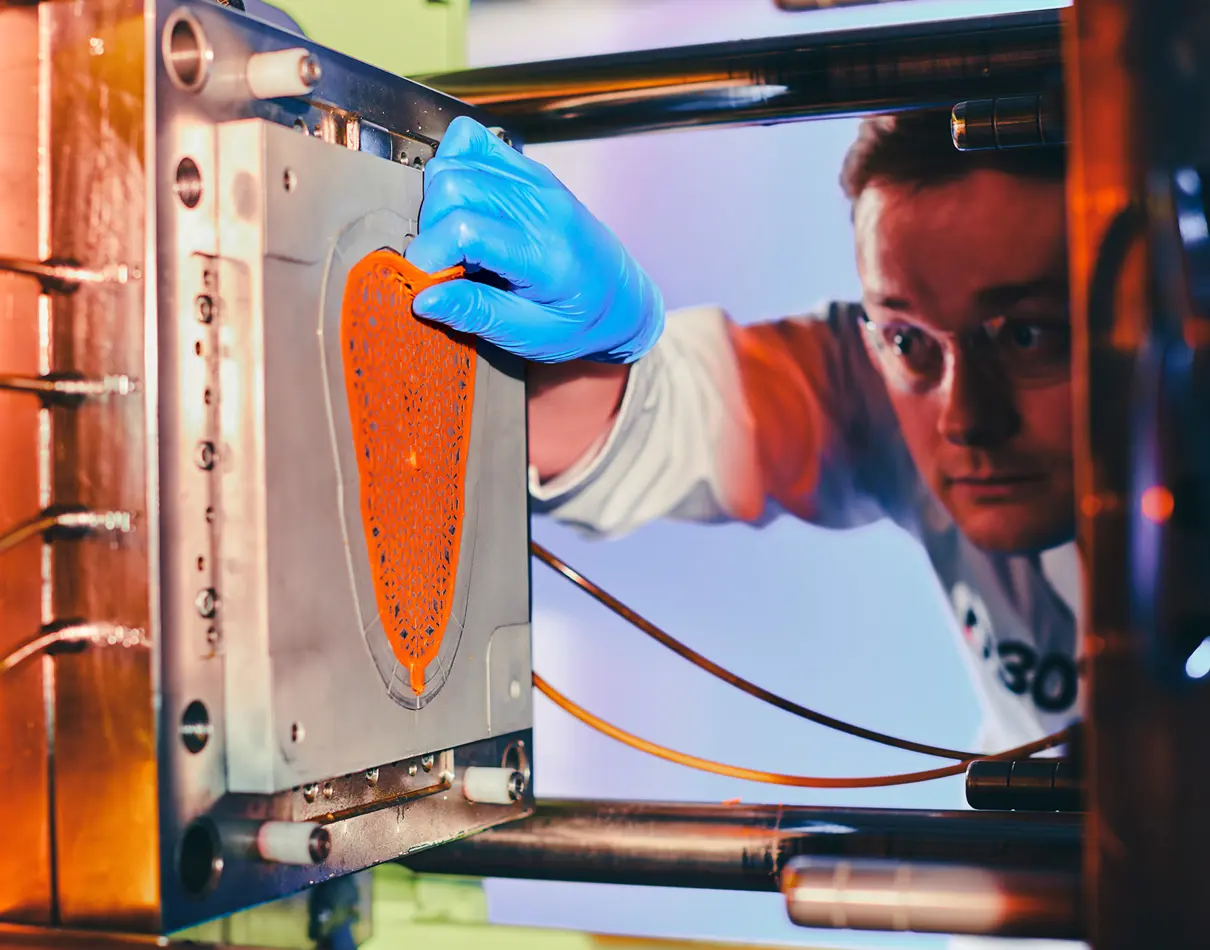
Best Mountain Bike Knee Protection
Fails are part of the fun of mountain biking, but that doesn’t mean your knees can’t stay protected. Find out how in this D3O article.
Read More
Are Mountain Bike Knee Guards The Same As Knee Pads?
If you’re wondering what the difference between knee guards and knee pads is, the impact protection experts at D3O have you covered in this article.
Read More
10 Best Mountain Bike Trails in the US
Want to know some of the best trails for mountain biking in the US? D3O has tracked down 10 of the best so you can get some incredible rides lined up.
Read More
How To Get Into Mountain Biking
Thinking of getting started with mountain biking? Find out what you need to know about getting into this thrilling sport and beginner set ups with D3O.
Read More
Mountain Bike Tips for Beginners
Are you new to mountain biking and looking to get some tips and advice for beginners? Check out this article from the impact protection experts at D3O.
Read More
Best Mountain Bike Shoulder Protection
Choose mountain bike gear with D3O shoulder protection for maximum safety, wearability and comfort.
Read More
Why Do You Need Gloves For Mountain Biking?
Up your mountain biking game with specialist gloves designed for taking on the trails. Find out how mountain bike gloves protect you on your ride.
Read More
Best Mountain Bike Elbow Pads
Mountain bike elbow pads help to protect riders from bruises and worse. Get tips on how to find the best option for your riding style in this D3O article.
Read More
A Guide To Elbow Pads For Mountain Bike Riding
Elbow pads are essential safety gear for mountain bikers. Find out about them and how to find the right ones in this D3O article.
Read More
What Shoes To Wear While Riding A Motorcycle
Motorcycle shoes keep your feet and ankles supported and protected as you ride, so it's important you wear the right ones to keep you safe. Find out the best options in this D3O article.
Read More
Best Motorcycle Shoes For Summer
Your feet need to stay protected and comfortable as you ride, especially in summer. D3O is here to help you find the best motorcycle shoes for summer.
Read More
How to choose motorcycle gloves
Get clued up on how to choose the right motorcycle gloves for your ride, including impact protection from D3O, fit, style, and comfort.
Read More
How Tight Should a Motorcycle Jacket Fit?
Get the perfect fit with your motorcycle jacket, ensuring maximum safety, comfort and cool while out riding, thanks to the experts at D3O.
Read More
Women’s Motorcycle Jackets With Armor
Female motorcyclists can choose a jacket designed specifically to fit women’s bodies without compromising on safety or style.
Read More
Summer Motorcycle Jackets With Armor
Stay cool and safe this summer by choosing a D3O-protected motorcycle jacket best suited for hot weather and humid temperatures.
Read More
Can you get stylish leather motorcycle jackets with armor
Leather jackets are a signature biker style but remember to prioritize safety when looking for a new motorcycle jacket. Learn more about D3O protected armored jackets.
Read More
What Is The Best Armored Motorcycle Jacket?
Armored motorcycle jackets help motorcyclists stay safe and stylish. Find the ideal one for you and your riding style in this D3O article.
Read More
How To Fit Mountain Bike Shoes
Whether you’ve decided on buying mountain bike shoes or aren’t sure if they’re right for you, here are some recommendations from D3O on how to fit and buy.
Read More
Are Mountain Bike Shoes Necessary?
Weighing up the pros and cons of using mountain bike shoes? Find out why you need to keep your feet safe and secure on the trail with D3O.
Read More
The Best Mountain Bike Gloves To Keep You Safe
Protect your hands from injury, fatigue and general wear and tear with mountain bike gloves - discover more in this D3O article.
Read More
Top 10 Motorcycle Safety Tips
Staying safe while out on the roads, tracks, or trails is essential.
Read More
Best Motorcycle Race Tracks in the US
We've rounded up 8 of our favorite tracks in the US for motorcycle racing.
Read More
How To Get into Motorcycling
Find out how your can get into motorcycling.
Read More
Is Motorcycle Armor Necessary?
Armor is not just worn by professional racers, but by everyday and casual riders too.
Read More
Does Motorcycle Armor Work?
Read about the importance of motorcycle armor.
Read More
Motorcycle Armor CE Certification
Understand what CE certification for motorcycle armor means, and why you should always choose CE-certified D3O armor for the best in protection.
Read More
What Are The Best Motorcycle Riding Pants?
Motorcycle riding pants are essential for bikers’ protection and comfort. Get some tips on finding your ideal pair in this D3O article.
Read More
Motorcycle Pants: Finding the Perfect Fit | D3O®
Read More
Motorcycle Pants Buying Guide
Motorcycle pants help to keep riders safe and comfortable on the road. Find out how to find the ideal ones for you in this buying guide from D3O.
Read More
Top Motorcycle Events in The US | D3O®
Read More
Different Types of Mountain Biking
There are several styles and disciplines within mountain biking.
Read More
Motor Cycle Boots or Shoes | D3O®
Read More
Biggest Motorcycle Races in The World | D3O®
Read More
What is Downhill Mountain Biking
Read More
What Is Enduro Mountain Biking
Read More
What is Cross-Country Mountain Biking
Read More
Shut the City Down Ride
D3O Ambassador Allan Lane leads 1,500 bikers through the streets of Philadelphia.
Read More
Decrypting eco-materials in electronics protection
‘Green’ electronics protection is big business. Is it genuinely good for the planet and, just as important, is it good at protecting your devices?
Read More
Developing a Workwear Knee Pad That's Fit for the Job
D3O has created D3O TRX™, the world’s most advanced knee protection range, providing unparalleled comfort, stability and durability.
Read More
"D3O already saved my neck"
Freestyle athlete Ewa Stunts talks motorcycles, stunt riding and why she trusts D3O technology.
Read More
Protecting the future of American Football
Gamebreaker CEO Mike Juels explains how better protection for players will better protect the future of the game.
Read More
Gearing Up For The Ride
Motorcycling apparel should not be a one-off purchase. Ugrading the armor within is a way for riders to upgrade their protection too.
Read More
"Going out without the right gear isn’t worth it”
Atwyld's Anya Violet explains how a motorcycle accident reinforced help belief in impact protection.
Read More
Keeping kids safe on the pitch
Gamebreaker's new Aura headband featuring D3O® is aiming to tackle head injuries in soccer.
Read More
ISEA 138 - We answer your FAQs
Following the launch of ANSI/ISEA 138, D3O industry experts answer your questions about the new standard for back-of-hand-protection.
Read More
Showing page 1 of 1